Čelik

Čelik (nȁdo ili ocal)[1] je slitina željeza s ugljikom (od 0,008 % do 2,14 %[2][3]). Gotovo sva količina proizvedenog sirovog željeza iz visoke peći prerađuje se u čelik, jer su njegova mehanička svojstva mnogo bolja od svojstava željeza. Primjena željeza je prvenstveno u obliku čelika, a manje kao sirovog ili lijevanog željeza. Odlikuju se velikom čvrstoćom, tvrdoćom, žilavošću, mogućnošću lijevanja i mehaničke obrade, te velikom elastičnošću. Rabi se za izradu mostova, automobila, brodova, željezničkih vozila i pruga, golemih građevina, ali i za sitnice nužne u svakodnevnom životu poput igle ili spajalice. Čelik proizveden recikliranjem (olupina automobila, starih željezničkih tračnica i neupotrebljivih lokomotiva), čelik je za sutra – za budućnost. U čeličnim spremnicima može se skladištiti koncentrirana sumporna kiselina jer pasivira željezo, što je dokazano pokusom.


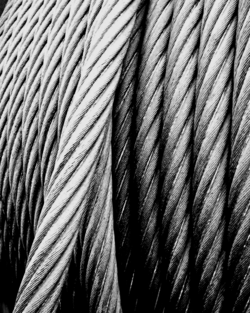
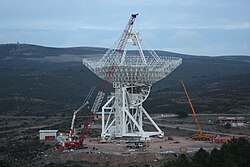
Proces prerade željeza u čelik je završen kada je postignut odgovarajući sastav taljevine. Tim postupkom nastaju takozvani ugljični čelici, neotporni na koroziju i visoke temperature. Najmoderniji način dobivanja čelika je u elektropećima (elektrolučna peć i elektroindukcijska peć). U njima se prerađuje i čelični otpad, kao i isluženi (izrabljeni) proizvodi od čelika i željeza. Dok se u posljednjih 30 godina proizvodnja „klasičnog“ čelika stalno smanjivala, rasla je proizvodnja elektročelika. Stručnjaci pretpostavljaju da će udio elektročelika u ukupnoj proizvodnji kroz sljedećih 10 godina biti iznad 50 %.
Za razliku od fosilnih izvora energije koji su se prije rabili i zagađivali okoliš, elektropeći imaju ekološki izvor energije (električnu struju), a i manje su i praktičnije od prijašnjih. Ova tehnologija omogućena je uporabom grafitnih elektroda jer grafit može podnijeti ekstremno visoke temperature u pećima. Kroz elektrode protječe struja jakosti 120 000 A. Pri temperaturi iznad 3 600 °C grafit sublimira, pri čemu ne nastaje ni pepeo, ni troska. Elektroda jednostavno ispari. Vrlo male količine ugljika oksidiraju se zrakom u ugljikov dioksid. Grafitne elektrode se nakon 24 sata istroše. Za jednu tonu čelika potrebno je 2,8 kg grafita.
Na taj se način dobivaju legirani čelici u kojima je maseni udio drugih metala veći od 5 %. Visoke temperature u elektropećima omogućavaju legiranje čelika s teško taljivim metalima, poput volframa (za vatrostalnost), molibdena (povećava tvrdoću i otpornost na koroziju), vanadija i kobalta.
Postoje različiti načini prerade željeza u čelik. Jedan od njih je postupak s čistim kisikom, w(O2) = 99,99 % (LD postupak). Kisik se upuhava kroz vodom hlađenu kopljastu cijev pod visokim tlakom, što dovodi do snažnog miješanja taljevine. U burnoj reakciji oksidiraju se primjese. Plinoviti ugljikov(IV) oksid i sumporov(IV) oksid izlaze iz taljevine, a teško hlapljivi fosforov(V) oksid i silicijev dioksid se dodatkom kalcijeva oksida izdvoje u obliku troske.
- 6 CaO + P4O10 --> 2 Ca3(PO4)2
- CaO + SiO2 --> CaSiO3
Podjela vrsta čelika
urediČelik se može podijeliti prema mnogim osnovama: prema postupku proizvodnje, prema kemijskom sastavu, mikrostrukturi, svojstvima, namjeni i dr.
Podjela čelika prema postupku proizvodnje
urediMasovna proizvodnja čelika je započela u 19. stoljeću otkrićem Bessemerovog i Thomasovog postupka. Čelik se danas proizvodi postupkom u konverterima s kisikom (LD postupak) ili u električnim pećima (elektrolučna peć, elektroindukcijska peć). U industrijski manje razvijenim državama još se koriste Siemens-Martinove peći. Osnovna sirovina za proizvodnju čelika u konverterima s kisikom je sirovo željezo. U električnim pećima pretaljuje se uglavnom stari otpadni čelik. Konvertor s kisikom i električna peć su uređaji za taljenje, a rafinacija taline (rafinacijski procesi) obavlja se u raznim reaktorima sekundarne metalurgije ili metalurgije u loncima, već prema svojstvu i kakvoći čelika.[4]
Prema kemijskom sastavu
urediPrema kemijskom sastavu čelici se mogu podijeliti na:
- Ugljični čelik: to je vrsta čelika u kojima odlučujući utjecaj na njegova svojstva ima ugljik, a drugih elemenata ima samo u količinama koje nemaju bitnog utjecaja i to: mangan < 0,8 % (maseni udio), silicij < 0,6 %, nikal < 0,3 %, bakar < 0,3 %, krom < 0,2 %, volfram < 0,1 %, molibden < 0,05 %, kobalt < 0,05 %, titanij < 0,05 % i aluminij < 0,05 %.
- Legirani čelik: to je vrsta čelika u kojima odlučujući utjecaj na njegova svojstva imaju legirni elementi, tj. oni kemijski elementi koji se namjerno dodaju da bi se postigla određena svojstva. Niskolegirani čelici imaju do 5 % dodanih elemenata, a visokolegirani više od 5 %.
Nehrđajući čelik
urediNehrđajući čelik je slitina željeza i najmanje 10,5 % kroma, i ne oksidira na zraku za razliku od običnog čelika (oksid je crvene boje), ako nije na neki zaštićen od korozije.
Prema namjeni
urediPrema namjeni čelici se mogu podijeliti na:[5]
- Konstrukcijski čelik: to je ugljični čelik (obični ili plemeniti) s udjelom ugljika manjem od 0,6 % ili legirani (uglavnom s manganom, silicijem, kromom, niklom, volframom). Koriste se za izradu čeličnih konstrukcija, sastavnih dijelova strojeva, aparata i različitih uređaja. Razlikuju se obični (ugljični ili niskolegirani) čelici za opću masovnu upotrebu i plemeniti (rafinirani) ugljični ili legirani čelici za dijelove s većim zahtjevima (dijelovi strojeva itd.);
- Alatni čelik: to je plemeniti ugljični ili legirani čelik s udjelom ugljika od 0,6 % do 2,06 % ili legirani (uglavnom s kromom, volframom, vanadijem, molibdenom, kobaltom), a koriste se za izradu alata;
- Specijalni čelik.
Prema mikrostrukturi
urediPrema mikrostrukturi čelici se mogu podijeliti na:
- Feritni čelik,
- Perlitni čelik,
- Martenzitni čelik,
- Ledeburitni čelik i
- Austenitni.
Željena se mikrostruktura postiže sadržajem ugljika i procesom direktne ili naknadne toplinske obrade.
Eutektoidni čelik
urediEutektoidni čelik je čelik s 0,8 % ugljika (masenih udjela), a naziva se i perlit. Perlit se sastoji od 88 % ferita i 12 % cementita (Fe3C). Eutektoidni čelik ili perlit ima u uvjetima polaganog hlađenja perlitnu mikrostrukturu, koja se sastoji od naizmjenično raspoređenih lamela ferita i cementita. Lamele ferita su oko sedam puta deblje od lamela cementita i mogu se vidjeti samo kod većeg povećanja optičkog mikroskopa.[6]
Podeutektoidni čelik
urediPolagano hlađenje podeutektoidnog čelika s 0,4 % C (masenih udjela) karakterizira sljedeće:
- na temperaturi iznad 800 ºC čelik ima austenitnu mikrostrukturu.
- na temperaturi malo iznad 723 ºC mikrostruktura čelika sastoji se od ferita s 0,025 % C i austenita eutektoidnog sastava s 0,8 % C. Ferita ima 51,6 % i austenita ima 48,4 %.
- na temperaturi ispod 723 ºC austenit eutektoidnog sastava raspada se u perlit, pa se mikrostruktura sastoji od 51,6 % ferita (proeutektoidnog) i 48,4 % perlita. Ferita ima 94,4 % i cementita ima 5,6 %. Na osnovi ovih podataka može se zaključiti sljedeće: 94,4 % ferita sastoji se od 51,6 % proeutektoidnog ferita i 42,8 % eutektoidnog ferita, a 48,4 % perlita sastoji se od 42,8 % eutektoidnog ferita i 5,6 % cementita (Fe3C).
Kada se podeutektoidni čelik hladi polako ispod 911 ºC dolazi do precipitacije ferita na granicama austenitnog zrna. Ako je hlađenje brže ili su zrna austenita jako velika, ferit koji je kristalografski orijentiran kao i austenit, više neće precipitirati na granicama austenitnog zrna kao ekviaksijalna zrnca, već u obliku iglica ili pločica, pa nastaje tzv. Widmanstattenova struktura ili Widmanstättenove figure.
Nadeutektoidni čelik
urediPolagano hlađenje nadeutektoidnog čelika s 1,2 % C (masenih udjela) karakterizira sljedeće:
- na temperaturi iznad 840 ºC čelik ima austenitnu mikrostrukturu.
- na temperaturi malo iznad 723 ºC mikrostruktura se sastoji od austenita i sekundarnog cementita, koji se izlučuje na granicama austenitnog zrna. Austenita ima 93,2 % i cementita ima 6,8 %.
- na temperaturi malo ispod 723 ºC austenit eutektoidnog sastava raspada se u perlit, pa se mikrostruktura čelika sastoji od 93,2 % perlita i 6,8 % proeutektoidnog cementita. Ferita ima 82,3 % i cementita ima 17,7 %. Na osnovi toga može se zaključiti sljedeće: 93,2 % perlita sastoji se od 82,3 % ferita i 10,9 % cementita (Fe3C), a 17,7 % cementita sastoji se od 10,9 % eutektoidnog cementita i 6,8 % proeutektoidnog cementita.
Prema načinu prerade
urediPrema načinu prerade čelici se mogu podijeliti na:
- Sirove čelike,
- Lijevane čelike,
- Valjane čelike,
- Kovne čelike,
- Vučene čelike, itd.
Povijest i današnja proizvodnja čelika u svijetu
urediČelik je bio poznat već u antičko doba. Najstariji otkriveni čelični predmet pronađen je u Anatoliji, starost mu je procijenjena na 4.000 godina.[7] Povijest metalurgije željeza započinje još u prapovijesno doba, ali se ne zna je li prvo željezo proizvedeno slučajno, kad je prapovijesni čovjek naložio vatru na ležištu čiste željezne rude ili je koristeći se već stečenim iskustvom u topljenju bakarne rude primijenio isti postupak na željeznu rudu. Taj postupak je bio prilično jednostavan: u plitkom ognjištu se željezna ruda pokrila drvenim ugljenom, koji se zatim zapalio, pa je ispod vatre nastala gnjecava i spužvasta željezna masa (spužvasto željezo). Da bi se iz spužvastog željeza dobilo tehničko željezo ili čelik ovisilo je prije svega od kvalitete željezne rude.
Plitko ognjište je bilo vrlo jednostavne konstrukcije. Sastojalo se od gnijezda oslonjenog na jedan zid, kroz koji je prolazila mlaznica mijeha za raspirivanje vatre. Gnijezdo se je ispunilo izmjenično slojevima željezne rude i drvenog ugljena, koji su se zatim zapalili. Puhanjem zraka kroz mijeh povisila bi se temperatura, tako da bi iz drvenog ugljena nastajao ugljikov monoksid, koji je vezao kisik iz željezovih oksida (uglavnom hematit), te se dobivalo spužvasto željezo i ugljikov dioksid. Pri tome je dobar dio željeza i dalje ostao vezan s kisikom (željezovi oksidi), te zajedno s nečistoćama kao tekuća troska otjecao iz ognjišta. Spužvasto željezo se skupljalo na dnu ognjišta sve dok ga ne bi potpuno ispunilo, pa bi se izvadilo i kovanjem bi se istiskivali ostaci troske i nečistoća (kovano željezo). Omjer između težine željezne rude i drvenog ugljena je bio otprilike 1 : 4. Ovim postupkom se dobivalo tek oko 12,5 % željeza iz željezne rude, a težina spužvastog željeza je iznosila do 70 kilograma. Ovakva plitka ognjišta su se održala u Štajerskoj i Šleziji sve do 18. stoljeća.[8]
Svjetska proizvodnja čelika iznosila je 2011. oko 1490 milijuna tona. Kina je prema podacima iz 2011. najveći svjetski proizvođač čelika (683,3 milijun tona) s oko 45,9 % ukupne svj. proizvodnje.
Poveznice
urediIzvori
uredi- ↑ http://hjp.znanje.hr/index.php?show=search_by_id&id=f1tuWRk%3D
- ↑ Iron-Carbon Phase Diagram Explained [with Graphs]. Fractory (engleski). 10. ožujka 2020. Pristupljeno 27. siječnja 2021.
- ↑ R, Rajesh Kumar. 1. kolovoza 2020. Basics of Mechanical Engineering (engleski). Jyothis Publishers. ISBN 978-93-5254-883-5
- ↑ "Tehnička enciklopedija", glavni urednik Hrvoje Požar, Grafički zavod Hrvatske, 1987.
- ↑ "Strojarski priručnik", Bojan Kraut, Tehnička knjiga Zagreb 2009.
- ↑ [1] Arhivirana inačica izvorne stranice od 31. srpnja 2013. (Wayback Machine) "Metali", www.ffri.uniri.hr, 2011.
- ↑ [2][neaktivna poveznica] "Povijesni razvitak materijala", www.riteh.uniri.hr, 2011.
- ↑ [3] Arhivirana inačica izvorne stranice od 4. srpnja 2014. (Wayback Machine) "Fizikalna metalurgija I", dr.sc. Tanja Matković, dr.sc. Prosper Matković, www.simet.unizg.hr, 2011.
- "Svojstva i primjena materijala", Filetin, Kovačiček, Indolf, Zagreb 2002.g.,
- Udžbenik za treći razred gimnazije „Anorganska kemija“, Sandra Habuš – Dubravka Stričević – Vera Tomašić. Izdavač: PROFIL INTERNATIONAL, tisak: tiskara Meić, Uporabu udžbenika odobrilo je Ministarstvo prosvjete i športa Republike Hrvatske rješenjem KLASA: *, od 3. Srpnja 1998.g.
Vanjske poveznice
urediOstali projekti
urediZajednički poslužitelj ima još gradiva o temi Čelik |